Starch processing industry - Thai raw starch and modified starch control system
Oxidized starch is one of the highest yielding products derived from cassava starch (original starch), which has some characteristics such as low viscosity, high stability, high transparency, and strong forming ability. Oxidized starch is usually formed by the reaction of cassava with hypochlorite under alkaline conditions.

Based on the characteristics of each process section and the monitoring function of the control system, this control system uses an industrial control computer as the upper computer, a DCS center controller as the lower computer, on-site sensors (such as temperature, liquid level, pH value, flow rate, etc.) and actuators (valves, pumps, motors, frequency converters, etc.) as monitoring points. Through communication between the upper computer and the lower computer, all monitoring points on the production line are recorded, displayed, analyzed, counted, queried, and controlled, thus forming an intelligent modified starch monitoring system.
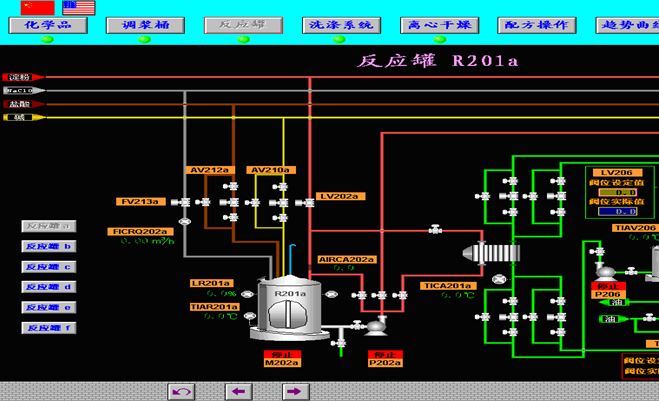
The DCS module is responsible for controlling and collecting data for each section, while the upper computer is responsible for data statistics and analysis, displaying process flow diagrams of measurement point parameters, control circuit and parameter setting screens, recording and displaying historical trends of main process parameters, recording parameter alarms, displaying, starting and stopping operation and monitoring screens, system self diagnosis screens, and other functions.
In order to ensure the normal operation of the operating system in the event of a malfunction, the system adopts redundancy between the upper computer and the central controller. In a dual machine redundant system, disturbance free switching has been achieved by transferring parameters from the running machine to the redundant machine, achieving complete tracking of the running machine by the redundant machine. Parameter transmitters are used for implementation.
The system has process flow diagrams, historical trend screens, regulator screens, event recording, alarm, user login and other screens.
Dynamic data: displayed at the corresponding location on the flowchart.
Link to dynamic images: make buttons on each image, click the button to pop up the corresponding image; Click on the regulating valve on the process flow diagram to bring up the regulating screen, where you can modify the given value, range, output value, and adjust PID parameters online.